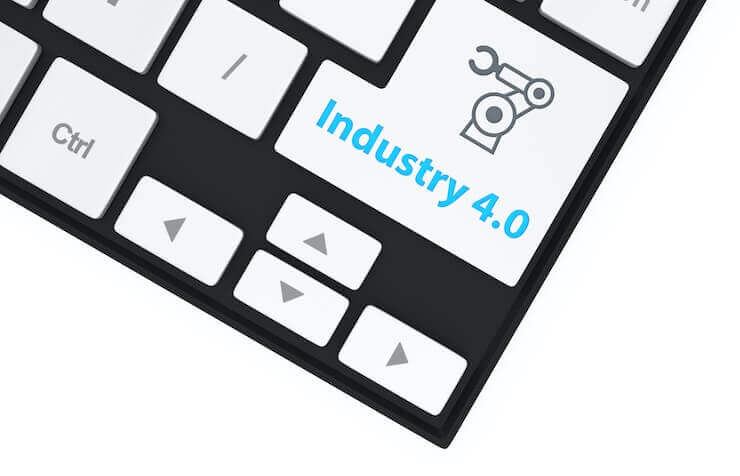
Plug & Produce(プラグアンドプロデュース)とは、生産設備と上位システムを接続し、相互に通信しながら効率的に生産する仕組みのことです。「インダストリー4.0」や「ファーマ4.0」の前提条件となるため、導入を検討している製薬企業も少なくありません。そこで今回は、Plug & Produce(プラグアンドプロデュース)の意味やメリットについて解説します。具体的な接続手法についても紹介しますので、ぜひ参考にしてみてください。
目次
Plug & Produce(プラグアンドプロデュース)とは?
そもそもPlug & Produce(プラグアンドプロデュース)とは、どのような意味なのでしょうか。
「インダストリー4.0」「ファーマ4.0」との関係性も含めて、解説します。
(1)Plug & Produce(プラグアンドプロデュース)の意味とは?
Plug & Produce(プラグアンドプロデュース)とは、Plug(つないで)・Produce(生産する)という言葉どおり、上位システムと生産装置をネットワークで接続し、相互に通信させて効率的に生産することを意味します。
そもそもPlug & Produce(プラグアンドプロデュース)の本質は、「システム同士のスキマ」「システムと生産装置のスキマ」を埋めることにあります。というのも、従来の製薬工場ではシステムと生産装置がつながっていないケースが多く、「システムからの製造指示を生産設備に手入力しなければいけない」「生産設備の状態がリアルタイムに分からずリスク管理が難しい」といった問題を抱えていました。ですが、システムと生産設備が直接通信することで、工場内の情報が一元化されます。結果として、手入力による工数が削減されるだけでなく、工場の状況をリアルタイムに把握することが可能になるのです。工場内の“スキマ”を埋めることで、管理の効率化や生産性の向上を実現することが、Plug & Produce(プラグアンドプロデュース)の目的と言えるでしょう。
(2)インダストリー4.0・ファーマ4.0との関係性とは?
「インダストリー4.0(Industry4.0)」とは、スマートファクトリー化を実現し、高品質な製品をより高効率で生産するための取り組みを指します。第三次産業革命(インダストリー3.0)の進化形という意味合いを持ち、ドイツが国家的に推進しているプロジェクトです。インダストリー4.0によるIIoT化は世界の製造業で徐々に浸透していますが、製薬業界では法規制の厳しさから導入が難しいのが実情でした。そこで、製薬業界において高度な規制に対応する形でスマートファクトリー化を進めようとする取り組みが、「ファーマ4.0(Phama4.0)」です。
インダストリー4.0・ファーマ4.0に共通しているのは、生産の全工程をネットワークで接続することです。システムと生産機器の相互連携によって、生産の効率化や自動化をかなえます。つまり、Plug & Produce(プラグアンドプロデュース)は、インダストリー4.0・ファーマ4.0を実現するための「前提条件」とも言えるでしょう。
Plug & Produce(プラグアンドプロデュース)のメリットとは?
Plug & Produce(プラグアンドプロデュース)を行うと、製薬企業にとってどのようなメリットがあるのでしょうか。ここでは、医薬品製造においてPlug & Produce(プラグアンドプロデュース)を実行し、スマートファクトリー化・IIoT化することのメリットを大きく3つ紹介します。
(1)工場全体を見える化できる
工場内がネットワークでつながることで、生産状況をリアルタイムに可視化できるようになります。例えば、わざわざ生産設備のもとへ確認に行かなくても、手元のタブレットやモニターで生産状況を把握することが可能です。仮に生産設備に異常が発生した場合は、アラームで察知してすぐに処置・改善を行うこともできるでしょう。このように工場全体を見える化することで、管理効率が高まり、リスクを最小限に抑える効果も期待できます。
(2)効率的な生産計画を立てられる
工場内をネットワークで接続することで、情報の分析がスムーズになります。例えば、重要工程パラメータや生産量のデータ、各装置のアラーム発出状況などを一括収集・分析することが可能です。こうした豊富なデータを活用することで、より効率的な生産計画を立てられるでしょう。また、システムと生産装置が自動で通信を行うため、人が行う作業も削減できます。作業の工数が減ることで、省人化による高効率化も期待できるでしょう。
(3)データインテグリティに対応しやすくなる
データインテグリティとは、すべての記録に一貫性・整合性があり、欠損がないことを意味する概念です。患者の生命や健康を守るため、医薬品製造の現場においては特にデータインテグリティの確保が求められています。
Plug & Produce(プラグアンドプロデュース)によって、データインテグリティにもスムーズに対応できるようになります。というのも、従来は生産工程に関する重要な情報が生産設備ごとに保存されているのが実情でした。情報の書き換えや修正も、さまざまな作業者が各生産設備で行います。その場合、情報に不整合や欠損が生じかねません。そこで、各生産設備を接続して情報を一元化できるようにすれば、すべての記録を時系列で管理することが可能です。結果として、データインテグリティで求められる「ALCOA要件」も満たしやすくなります。
※データインテグリティについて詳しく知りたい方は、「データインテグリティ(DI)とは?対応が必要な理由と対策を分かりやすく解説!」も合わせてお読みください。
※ALCOAについて詳しく知りたい方は、「「ALCOA」「ALCOA CCEA」とは?対応のポイントも合わせて解説!」も合わせてお読みください。
Plug & Produce(プラグアンドプロデュース)の具体的な仕組みとは?
医薬品製造の現場でPlug & Produce(プラグアンドプロデュース)を実行するには、具体的にどのような仕組みが必要なのでしょうか。ここでは、代表的な構成と必要なシステム・ネットワークなどについて説明します。
(1)全体像について
Plug & Produce(プラグアンドプロデュース)を実現するには、上位システムと生産装置をネットワークで結ぶ必要があります。具体的には、ERP(統合基幹業務システム)・MES(製造実行システム)・SCADA(監視制御ソフトウェアプラットフォーム)・PLC(生産設備の制御装置)・各生産設備を産業用イーサネットで接続します。こうしてシームレスな通信で工場内の垂直統合を図ることで、リアルタイムな情報収集・生産管理が可能です。
※各システム・装置の意味については、以下(2)~(6)にて説明します。
(2)ERP
ERP(Enterprise Resources Planning)は、統合基幹業務システムを指し、会計や生産、販売などの各情報を統合管理するシステムのことを言います。経営戦略を立て、ヒト・モノ・カネ・情報などのリソースをどう配分するか決定する際に活用されます。経営の中枢を担うシステムとして、垂直統合において最上位に来るイメージです。
(3)MES
ERPの下位で接続されるのが、MES(Manufacturing Execution System)です。MESは製造実行システムと訳され、製造工程の管理や作業者への指示出しなどを行ってくれます。具体的には、作業のスケジュール管理や各バッチの作業指示の立案、作業状況の把握、実績分析やレポーティングなどの多様な役割を担うシステムです。
(4)SCADA
Plug & Produce(プラグアンドプロデュース)において情報の“ハブ”としての役割を果たすのが、SCADA(Supervisory Control And Data Acquisition)です。SCADAは「監視制御とデータ取得システム」とも訳され、各生産装置のセンサーから送られてくる情報を監視制御しながら、データの蓄積・分析を行ってくれます。
製薬工場では、MESと生産装置が接続されていないケースも少なくありません。ただその場合、MESの生産指示を人が印刷し、生産装置まで出向いてPLCに手入力するという工数が発生します。ここでMESとPLCの間にSCADAを導入することで、人の手を介さなくてもデータの相互通信が可能になります。つまり、SCADAによって手入力による工数を減らしたり、データインテグリティの確保に必要な情報を一元管理できたりするのです。
(5)PLC
PLC(Programmable Logic Controller)とは、機械の制御装置を意味します。具体的には、各生産設備の入力・出力を管理したり、データの演算を行ったりする装置です。基本的にPLCはそれぞれの生産設備に対して設置されており、制御を担っています。大規模な工場になると数多くの生産設備が稼働しているため、その分PLCの持つ情報も膨大です。そこで、SCADAが各PLCからの情報を一元化し、管理する役目を果たしてくれます。
(6)産業用イーサネット
システムや装置を接続するには、通信手段が必要です。ただ、生産工程ではさまざまなアプリケーションインターフェースが存在し、通信方式も混在しています。特にPLCより下位の層は通信にリアルタイム性が求められ、かつメーカーによって通信プロトコルが異なるため、接続は容易ではありません。そこで、今では「産業用イーサネット」と呼ばれる通信方式が使われています。産業用イーサネットとは、上位システムで使用されるイーサネットを下位層でも対応できる方式へ拡張したもので、システム・設備間のシームレスな通信が可能になります。産業用イーサネットには複数の種類があるため、既存システムや機器の規格に合わせて選ぶことが大切です。
Plug & Produce(プラグアンドプロデュース)の対応には、最適なシステムの活用を
Plug & Produce(プラグアンドプロデュース)では、使用システムや生産設備の通信プロトコルなどにより、導入すべきソリューションが変わってきます。そのため、まずは自社の現状を深く理解することが大切です。そのうえで、IT・OT担当者が連携して対策を進めることをおすすめします。
ちなみに日本の製薬現場では、MESと各製造装置がネットワーク統合されておらず、それぞれが独立している現状が多く見られます。「MESから出力した製造情報を各装置へ入力する」という手間が発生し、打ち込み作業で時間がかかることでヒューマンエラー発生の可能性も考えられます。これはデータインテグリティ対応の観点でも、決して十分とは言えません。
そこで当社では、製薬工程におけるあらゆる情報を一元管理できる情報統合システム「FIDIUS」を提供しています。当システムが「ERP」「MES」などの上位システムと生産装置とを統合する役目を果たし、工場内のPlug & Produce(プラグアンドプロデュース)を実現。また200社を超えるPLCメーカーとの接続が可能なので、スムーズな導入につなげられます。Plug & Produce(プラグアンドプロデュース)の具体策を検討される際には、ぜひ当社までお問い合わせください。